同じ部品を複数個作製する場合、真空注型が有効な場合があります。
真空注型とは、光造形品や切削加工品をマスターモデルとして硬質または軟質のウレタンで複製品を作る工法です。
製造の流れ
マスターモデルの形状をシリコンに反転し型を作製します。
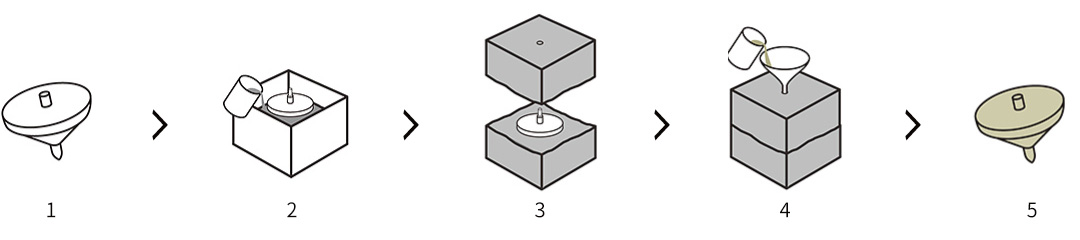
1. 光造形でマスターを作製
2. 型枠にシリコーンを流す
3. 型を割りマスターを取り出す
4. 樹脂を流し込む
5. 型から取り出し仕上げをする
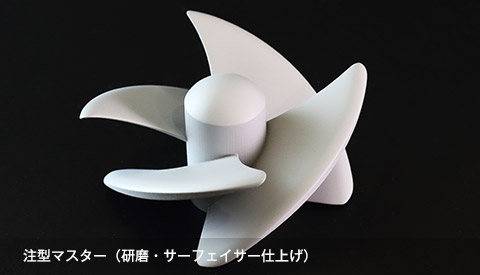
小ロット量産
元となる製品があればモデルの複製が可能です。マスターモデル1個の表面を仕上げることで、真空注型品全てにその表面状態が反映されるため、小ロットの量産において時間とコストを抑えることが可能です。
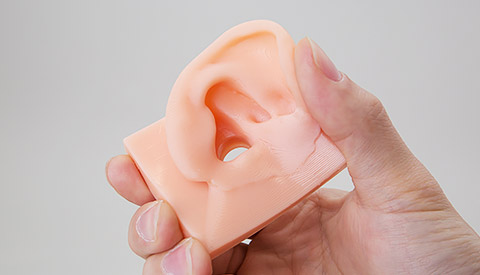
自由度
軟質のシリコーン型を使用するため、多少のアンダーカットであれば型割りを増やすことなく複製可能です。またある程度の硬度調整や着色が可能です。
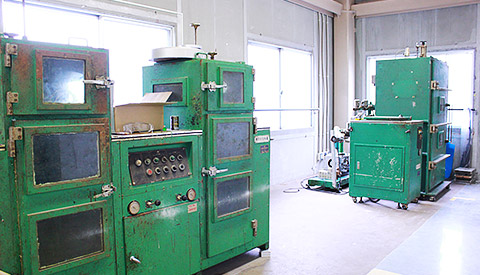
インサート可能
注型時、型に別部品(金属ナットや端子など)を配置することでインサート注型が可能です。