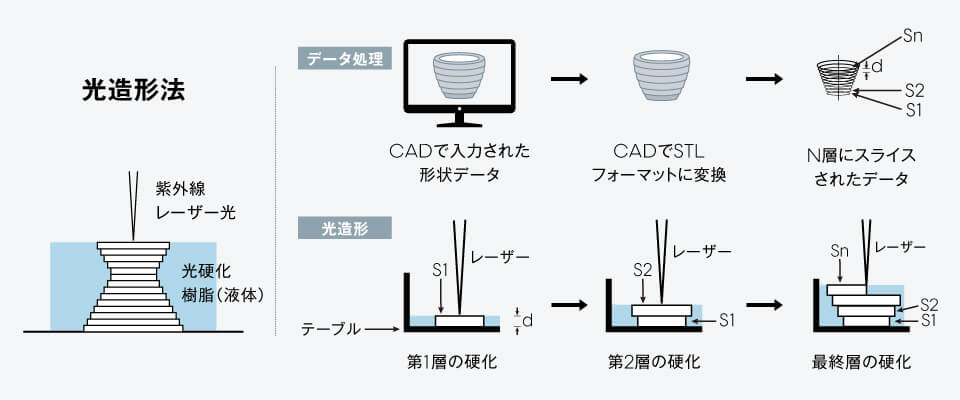
光造形技術(SLA、DLP、LCD)は、光を当てると液体から個体に変化する材料、光硬化樹脂を用いて、光を細かくコントロールしながら積層造形します。3Dプリンティングの中でも特に高精度で滑らかな表面仕上げを実現できる方式です。その歴史的背景には、日本人エンジニア小玉秀男氏の貢献が大きく、1981年に彼が光硬化性樹脂を用いた3D造形法を発明しました。これが光造形技術の基本となり、その後、1986年にアメリカのチャック・ハルがこの技術を基にしたSLA(Stereolithography)技術を発展させ、3Dプリントの商業化に成功しました。
SLA技術の特性
SLAは光造形全般を指す言葉でしたが、現在は光造形の工法が増え、光造形の中でレーザー光を使う装置分類をさします。高額であるため導入のハードルが高いと言えます。トップダウン方式という造形方法を採用している装置では、造形物を液体樹脂に沈めながら積層を行うため、重力の影響を軽減し、安定した造形が可能です。このため、一度に大量のモデルや大型のモデルを製作することが可能であり、特に産業用途に適した装置とされています。
SLA装置は、精度と安定性が重要視される産業分野で利用されることが多く、産業用として位置づけられています。運用にはレーザーの制御やサポート付けなどの専門知識が必要であり、これに伴う教育や人的コストも考慮する必要があります。
造形プロセスと精度
《CMET ATOMm-8000》
紫外線硬化の液体エポキシ樹脂に紫外線レーザーを照射することによって硬化、積層させることでモデルを作製します。仕上がりは透明または半透明です。
1.紫外線レーザビームで樹脂液面を断面形状通りに走査することにより、表層の硬化と下層との接合を行います。
2.一層の厚さ分だけ、テーブルを下降します。
3.できた硬化層の上に材料樹脂を薄く塗ります。
4.1、2、3 を繰り返すことにより、モデルを作製します。
寸法精度
外寸100mmのモデルであれば横XY方向:±0.10mm ~ ±0.15mm 程度です。材料である光硬化性樹脂は硬化時に収縮し、一層の断面積が大きい程収縮は大きくなります。
積層について
積層厚0.10mm、0.15mm、0.20mmでの作製が可能です。
長所
造形サイズ
光造形の中では、SLAのトップダウン方式(自由液面方式)が安定して大きな造形が可能です。液中での積層造形は、重力の影響を 軽減し、造形の安定性が高いです。そのため造形途中で破綻することが少なく大物の造形が可能です。
精度・微細形状の再現
紫外線硬化のため、熱溶融積層法や粉末焼結方式に比べて収縮・硬化時のそりは比較的少ないです。また造形中の精度はレーザーを反射するミラーの稼働の細かさ(ガルバノメーター解像度)に依存します。装置によって異なりますが一般的に10~100μm(0.01~0.1mm)の範囲で動作します。
精度・微細形状の再現
紫外線硬化のため、熱溶融積層法や粉末焼結方式に比べて収縮・硬化時のそりは比較的少ないです。
また造形中の精度はレーザーを反射するミラーの稼働の細かさ(ガルバノメーター解像度)に依存します。
装置によって異なりますが一般的に10 ~ 100μm(0.01 ~ 0.1mm)の範囲で動作します。
SLA 方式はレーザーが照射された箇所だけ硬化するので、最小サイズはレーザー径に依存します。
レーザー径は装置によって異なりますが、一般的に30 ~ 140μm(0.03 ~ 0.14mm)の範囲です。
イメージとして、SLAプリンターをペンとして置き換えると、レーザー径はペン先の太さ、ガルバノメーター解像度はペンを動かす精密なロボットアームの動きの正確さにあたります。ペン先が細ければ細いほど、そしてロボットアームが正確に動けば動くほど、細かい文字や絵を描けるようになるのと同じです。大きな装置程、スピードを速くするため、ガルバノメーター解像度とレーザー径は大きくする必要があります。
短所
メンテナンス
SLA 方式はレーザー光源の為、微調整には、専門的な知識と技術が必要になります。
サポートが必要
造形中にモデルを支えるためのサポートと呼ばれる構造が必要です。造形前処理として、データ上でサポートを設計する必要があり、 また造形後処理としてサポートを取り外す作業が発生します。
JMC主要設備
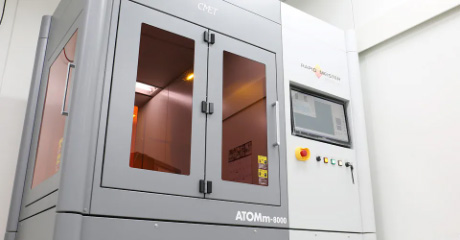
《光造形機 ATOMm-8000》
装置外寸1565×1050×1900mm
最大ワークサイズは、800×600×400mm
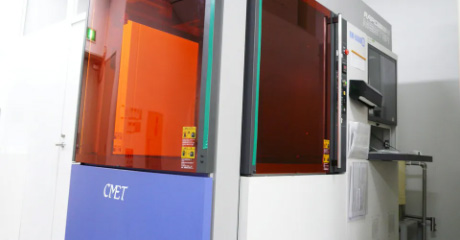
《光造形機 RM6000Ⅱ》
装置外寸1565×1050×1900mm
最大ワークサイズは、600×600×500mm
その他付随設備
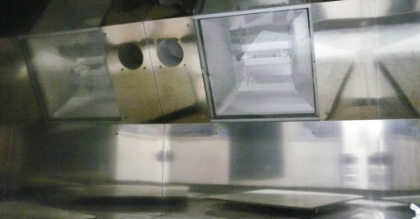
造形時にモデルは、材料の収縮による変形を防ぐために半硬化状態で造形されます。このためモデルの洗浄後には、紫外線ランプによって完全硬化させるポストキュアという処理を行います。JMCでは大型のポストキュア装置を導入しており、装置外寸は1300x1000x1600mmで、600mm角のモデルまでを入れることが可能です。内面は鏡張り、ステージはターンテーブルになっており、モデルを広範囲で一度に硬化させることが可能です。